Corbin makes the ET-2 Jacket Trim die sets for cutting bullet jackets to shorter lengths in a precise, rapid manner. The earlier ET-1 is still made on special order, as well. Copper tubing can be cut with a die, but it is generally more effective to use a tubing cutter saw.
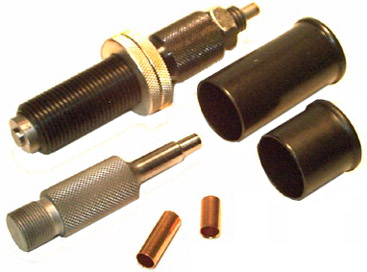
The ET-1 system uses a fixed length punch of two diameters. You need a specific punch for each length of jacket that you wish to make. However, it trims the surplus material completely away from the final jacket, so no manual separation is required. However, because the larger diameter of the punch must fit inside the jacket before trimming takes place, the jacket must either be pre-expanded to the distance of the trim, or it must start out as a larger jacket than you want and be drawn down during the trim.
Larger Jacket Reduction
If you have a jacket that can be reduced at least twice its wall thickness, then it is possible to build a single die that will both reduce and trim the jacket to a specified length. For example, to reduce from a .308 to a .284 is .014 inches of outside diameter reduction. If the walls of your .308 jacket are .007 or less, then it means the ID of the .308 jacket would be large enough to fit the .284 punch inside prior to drawing. But few .308 jackets are that thin. Most of them have closer to .020 inch walls (near the point of desired trim).This would mean that a stepped punch, with the top small enough to fit inside after drawing, but the bottom exactly the OD of the drawn jacket, would have to be .308 minus two times .020 inches, or .308 - .040 = .268 inches maximum size to fit inside this jacket. Therefore, you could not use this method of drawing and trimming for any caliber larger than .268 inches. You could use the 0.020 wall .308 jacket to make a .264, or a .257 trimmed jacket. But you could not make a 7mm (.284) or a .270 (.277).
Same Size Jacket
However, there is a trick you could use. Instead of drawing the .308 down with the stepped trimming punch inside it, you could pre-expand the jacket in another die, with a tapered punch. Then, you could use the stepped punch to draw and trim it, because the punch would now fit inside the expanded portion of the jacket. This is the 2-die method of using an ET-1. The expander die is necessary when you wish to use the same caliber jacket before and after trimming, or when the trimmed/drawn jacket will be within two wall thicknesses of the original diameter.In both cases, some kind of stripper assembly will be needed to pull the expanded jacket or the surplus material trimmed from the jacket off the punch. The pressure needed to expand or to pinch trim the jacket is enough to press the jacket tightly on the punch, so you probably can't remove it by hand. This is accomplished by making a snug fitted hole in a disk or a steel bar. The disk is used when you can drop a steel tube over the ram of the press for support on the down stroke. The bar is used in presses where the ram does not allow a tube over it, such as the Hydro Press or the Mega Mite press. In those presses, an ejector assembly that is suspended from the press head supports the bar, and stops it while the ram continues down, to strip the material from the punch.
As you can see, the ET-1 system consists of various components that may be required when using different jackets or presses. Sometimes it is one die, sometimes it is two dies, and usually it requires some kind of ejector mechanism (disk and tube, or the -H ejector system). The price will depend on the specific jacket and press you wish to use. It is best to discuss this and send sample jackets to get a quote.
About Corbin Bullet Jacket Trim Dies