The Base Guard bullet is made either in a LSWC-1 die (if you don't mind the shoulder of a semi-wadcutter design), or in a regular three-die set such as the FJFB-3 (for smooth ogive bullets).
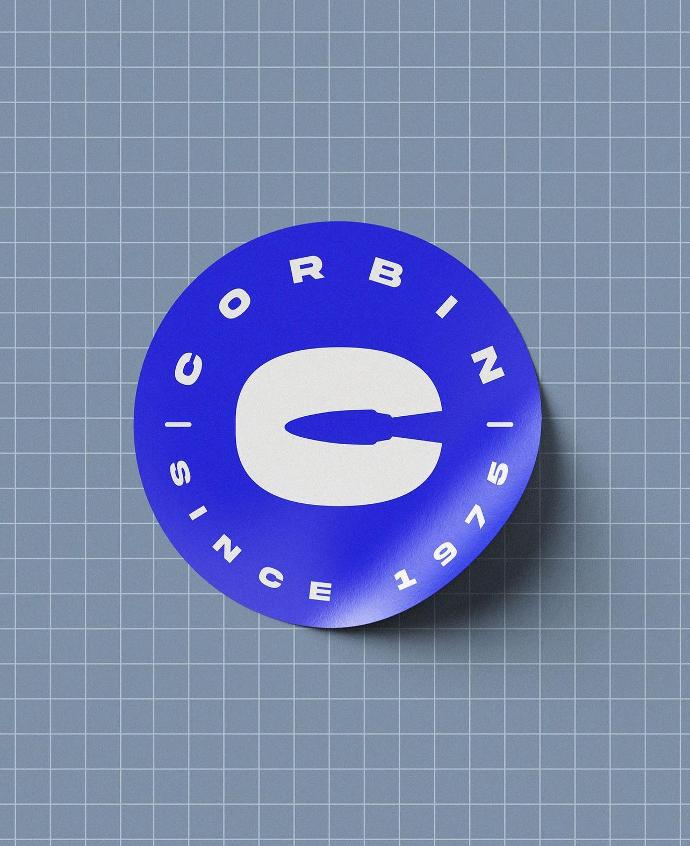
Base Guards are remarkable in their simplicity: a disk of copper, which starts out with a conical shape with a hole at the peak, is dropped into the die and a piece of lead is put on top of it. The assembly is squeezed under tons of pressure, flattening the disk and making it grow until it hits the die walls. Then it forms a forward-pointing scraper edge (burnishing tool edge) toward the softer lead and away from the hard punch. This edge, when driven down the bore, seals gas and removes leading from the bore. It is not necessary to use lubricant or hard lead with these bullets, even with velocities as high as 1,400 feet per second, in most guns.The conical shape of the BG disk is what makes it work so well. The idea of using a zinc washer was tried and used with limited success in the 1950's (see the Harvey Prot-X-Bore for more info). It turned out that the washers could not be cut precisely enough to seal the bore, and that one edge was always rounded while the other was sharp. If the bullet maker put the rounded edge toward the bullet, there was no scraping or burnishing action to clear the bore. Also, if the washer was even a few ten thousandths smaller than the bullet, gas would leak around it and melt the lead into the bore.
But making the BG disk undersized and conical solved the problems. First, the disk gets its final diameter by being flattened when it is attached to the bullet. This makes the disk grow in diameter until it contacts the die walls. Then the surplus metal is forced to extrude forward and form a burnishing tool edge, because it is supported on the other side by a solid steel punch and cannot move that direction. The only way it can move it toward the relatively soft bullet material. This is exactly what we want: a base that is exactly the diameter of the bullet, with a scraper edge facing forward to clean the bore when fired.
Because the BG disks are made undersized on purpose, they can be used in several close calibers. The .45 BG disk works in .458 rifle, .454 Long Colt, .452 for the .45 Auto, .454 Casull, and most other .45 pistols. The .44 works in .444 Marlin (.430-.431), .44 Mag and Special (.429) and similar .44's. The .40 works with all the .40 and 10mm pistol calibers. The .38 works for 9mm, .380, .38 Super (.354-.355 diam) as well as the entire range of .357 Mag and .38 Special calibers (.357). The .30 BG works for all the .32, 7.65mm, and .308-.312 pistols.The disks are available in bags of 1000, with price depending on the diameter and thus weight of copper in the package. When you consider the speed, ease and functionality, the Base Guard is probably one of the most cost-effective bullets you can make. It has been used for years in top level action pistol shooting, metallic silhouette pistol matches, and bullseye shooting as well as lead, blackpowder bullets for rifles like the .45-70 and .38-40.
Corbin also builds simple tools to punch your own precision base guard disks. All you need to use the disks is a swage die with a BG punch, which is a flat punch having a machined rivet head depression in the face. This is what forms the rivet of lead that holds the Base Guard disk on the base of the bullet and lets it turn to track the rifling, even if the bullet wants to skid.Copper Strip is available from Corbin for making Base Guards. The base guard disk works best when made of copper, or a zinc alloy containing not over 10 percent zinc and the balance copper. The minimum thickness for satisfactory work is .026-inches, and the maximum practical thickness is around 0.050-inches. The best thickness for economy and performance is 0.030-inches. The proper grade is non-earing, deep-drawing grade, annealed, edge-finished (no burrs), smooth finished surface. Lead flows through the hole in the base, and the stiffness of the material prevents it from bending back or extruding with the lead. If you use hard lead alloys, the pressure against the edge of the copper disk may become so great that it does push the copper back with the lead when forming the rivet head. This can cause the disk to be poorly attached with a malformed rivet head.
In experiments with very thin materials or with hard lead, we have found that the disks typically follow the bullet to the target, held on the base by the force of the base drag forces and carried along with the bullet even if not attached properly. However, just before striking a target, the turbulence at the base is increased by the shock wave reflected from the target, and the base slides to one side where it does not have time to turn sideways before cutting a perfect round hole in the target. The hole is virtually identical to the bullet hole, and usually occurs within an inch of the bullet impact. This can results in two shots scored for one fired, or it can be grounds for disqualification if the rounds are counted against the shooter. Be aware of the effect. This does not occur with proper lead softness or proper disk thickness.
The BGK-1 Base Guard Maker is available in three types:
All three dies work the same way. Copper strip is pulled through a slot in the die, under the press head. A punch moves up and down with the ram, just far enough to punch through the copper strip and lift the cut disk into the die bore. A stack of cut disks lift each other up through the die and out the top. The punch remains inserted and guided by the die during operation, to avoid striking the face of the die and snapping off the guide portion of the die at the slot.The BGK-1-R is slightly different from the dies for Corbin presses, because a reloading press generally does not have proper ram clearance at the top of the stroke for swage dies. In type -S and -H dies, the slot in the die is below the press head. The die is installed from the bottom, and is screwed upward into the press head (just the opposite of most dies that fit the press head). In the -R type, the slot is on top. The die is made extra large diameter to give it strength for cutting against the otherwise unsupported top end of the die. Using your -S or -H dies in this manner will cause them to snap off at the slot! Do not use the -S or -H type die with the slot on top of the press head. Doing so will void the warranty and probably break the die.
The lower portion of the die is a guide for the punch. It is only necessary to move the ram far enough to clear the slot so you can advance the copper strip, and then raise the ram just far enough to cleanly punch through the strip. This is a very short motion, usually less than half an inch. Therefore, you can adjust the die so that the copper strip is punched through at the top end of the stroke, just before the ram runs out of movement. This gives you much higher leverage and makes the operation easier than if you try to use the punch to push the cut disks all the way out the top of the die on every stroke.
The stack of cut disks in the top of the die will move out the top as you continue to cut more disks. If a disk tips sideways or jams, causing hard operation and excess effort, simply lower the die and push all the disks through to clear them, then adjust it back to the higher position again. A light film of Corbin Swage Lube wiped on both sides of the strip will help reduce friction and increase the life of the punch.Materials other than Corbin's .030-thick copper strip may cause a problem with improper shape due to the resistance to being punched. The small post in the punch contacts the strip first, and pushes a cone shape into the strip before it punches through. Since different materials may resist stretching or punch through either more easily or with far more force, it is possible that they might not form the cone, or might fail to punch out the small hole in the center of the disk.
Using iron or steel sheeting, or hard brass, may cause damage to the punch or die. Although other materials may work, it is best to use Corbin's CU-5 or CU-50 copper strip, which is a deep drawing grade with good surface finish and deburred edges, with proper anneal and good tolerance control. It is 0.030-inches thick with a 1-inch width. Small disks can be cut from one edge, and the strip turned over so that another row can be punched from the other edge. Larger disks may be economically cut by allowing a staggered double row, with the disk centers offset from one side to the other.
Start writing here...
About Corbin BGK-1 Base Guard Kits