Corbin has temporarily discontinued the offer of EZ-FLOW(tm) tungsten powder with 1% accra-wax coating on the grains, due to the high current price for tungsten. We provide Atomized Copper powder with 0.25% lithium stearate. The grain coatings help the materials flow smoothly without bridging and hanging up in powder dispensers, in funnels, or in drop tubes, reduce the drag and tendancy of the materials to "grab" the walls of their containers or dies under pressure, and finally, aid in allowing the microscopic "dust" to smoothly slide into close position and bind together under high pressure.
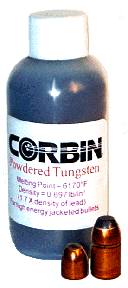
Until the recent market changes, Powdered tungsten was available from Corbin in 7000 grain, 35000 grain, and 70000 grain dispenser flasks. It may be offered again once the market stabilizes. EZ Pour Tungsten pours easily through a spout, and can be measured by weight or by volume. Powdered copper is available from Corbin in 1/2 pound, 4 pound, and 100 pound size containers. Three ways to measure powdered metals by volume are:
If you are using Corbin's Atomized Copper powder, you can swage bullets directly in the die without using a jacket, or you can pre-swage a copper core in a solid "core seating" type of die that is actually made in the diameter for a core swage (resulting pellet fits into the jacket, if one is to be used). However, the powder funnel with precision spout that matches the jacket wall thickness, and provides a straight path for the extra-long core seating punch for the powder column, will not work without the proper jacket in place. In that case, we suggest a custom die that has been machined to precisely align an extension section having a funnel-like bowl machined into the top. This extension fits on top of the core seating die, and allows the powder to stack up in a long column, which is then compressed into the lower portion of the die (normal length). The extension is then removed, and the bullet is ejected. Swaged powder usually will not bond together with additional loose powder. Adding more after swaging it usually results in two separate pellets that only appear to be one, but break apart easily. This may not be a problem with some designs (fragmenting, defense, or target bullets). In that case, you can add two separate "shots" of powder, swaging the first one down and then the second on top. However, if you must have the powder as one solid pellet after swaging, then the amount of powder initially compressed has to be the final weight desired in the pellet. To get it all into the jacket (assuming you are using a design that requires a jacket), you can preswage the pellet (or "core", as it would be called for bullet making purposes) in a smaller diameter die. This die can be a regular "core seating" die, without bleed holes (as the powder would tend to blow out the holes). However, it would need to have a hole size ("bore" or caliber) which would make a small enough core to fit inside the desired jacket. Jackets for a .30 caliber, for instance, could have a wall thickness from .015 to .035 inches thick (typical). Not only that, but they could taper in thickness from the mouth to the base. The solid core needs to be small enough so it fits all the way to the bottom of your selected jacket. This means that before you decide on a core seating die to make the powder metal pellet, you have to decide on a source of jackets and use them to determine the pellet diameter required. So, the first step is to decide upon a jacket. Making your own jacket from copper tubing is the most secure and versatile way to obtain bullet jackets today. You are independent of any manufacturers other than copper tube mills, of which over 200 operate in North America today. Tubing is used in such a wide range of applications, from air conditioners to power plants, from automobiles to steam boilers, that the chances of it becoming hard to find are extremely rare (provided you know where to look). Corbin supplies copper tubing in deep drawing grades, with high precision tolerances designed for jacket making, in all sizes from 1/4-inch diameter to 1/2-inch diameter. All standard calibers from the .224 to the .50 BMG can be made from this range, in just four sizes. Tubing is available from Corbin in 1/4-inch, 5/16-inch, 3/8-inch, and 1/2-inch diameters with a typical wall thickness of .035 inches. Experience has proven this wall thickness offers the best combination of big game hunting and precision target shooting characteristics, when combined with other techniques to enhance either the strength or increase the expansion. Corbin's tubing is a semi-hard drawn seamless lead-free copper available in two forms:
There are several ways to cut your own pieces of tubing to length before forming them into jackets (which rolls over one end and flattens it, or makes a rebated boattail if you wish). In order of desirability and quality of cut, these are:
The blade used to cut copper needs to have either a flat rake angle or even a reverse rake, and should have enough teeth per inch so that there are two or more teeth in the copper walls at all times. Special blades with proper rake and set for aluminum, plastic and copper are available for most power saws. Normal blades tend to grab, tear, and smear the copper because they plug up quickly with the soft, "sticky" chips. Copper tube will usually try to rotate when the teeth dig into it, so it needs to be held firmly against a fence or guide, or even clamped with a soft-jaw or contour-machined quick-clamp device while cutting. Most people have built their own additions to conventional saws to create accurate length stops and hold-down clamps. A standard tubing cutter will roll the copper so badly that it won't fit over the punches, and it is too slow and inaccurate. Once the copper tubing is cut to length, it is processed through a series of steps in one of Corbin's CTJM-1 tubing jacket makers. This rounds one end, draws the tube to exact size, flattens or boattails the end, and thus produces a "drawn-over-mandrel" precision jacket that is hard to tell from a factory jacket, except it is normally more effective for the purpose (since you build it exactly to desired length and style). With the jacket source secured, you are ready to work on the filling or core. The ID of the final jacket will be somewhat different than the theoretical dimension, depending on variables such as jacket compression and plastic flow. You may be able to guess by simply subtracting twice the jacket wall thickness from the caliber, but it usually is off by several thousandths. The only sure way to know the proper core size is to make some jackets and measure them. ![]() Atomized copper is available in 8-oz, 64-oz, and 100-lb packages from Corbin. ![]() | Corbin can provide powdered metal measure/dispensers mounted on quick-adjustable arms, for any of our presses. Shown below is a measure mounted on the CHP-1 Hydro Press. Corbin powdered metals are sold in 2-fluid-ounce or 8-fluid-ounce containers with dispenser caps. Actual weight of the metal will vary with its density. For example, the 2-fluid-ounce container of tungsten weighs one pound, whereas the 2-fluid-ounce container of copper would weigh about 8 ounces. Larger quantities are also available.
Mohs Hardness Index
| |||||||||||||||||||
Knowing the proper jacket ID means you can determine the size of the core to fit inside. The core should slip easily into the jacket, so it can be anywhere from 0.002 to 0.010 inches smaller than the ID of the jacket. For instance, a typical .308 tubing jacket might have an ID of 0.235 inches, which means that the pellet or core could be from 0.233 to as little as 0.223 inches in diameter. It cannot be the same size, because even if you could force it in, air might be trapped inside like a pistol and cylinder. |
|
World Leader in Swaging Technology Since 1975
Start writing here...
How To Make Powder Metal Bullets