You can make FREE 22 caliber centerfire bullets using recycled materials (fired 22 cases and range lead or soft lead wheel weights) using either your existing 7/8-14 reloading press, or a Corbin Swage Press. Here are the steps for either press.
The Corbin Swage Press is 300% faster, and can be easily expanded to make other calibers from .104 to .458 diameter later, if you wish. It comes with free reloading adapter to use your existing 7/8-14 reloading dies and button shell holders, providing super-powerful, benchrest precision replacement for an over-the-counter, mass produced single station reloader.
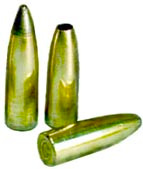
Here are two complete kits: KIT-224R for your reloading press, and... KIT-224S for the Corbin S-press (CSP-1). |
![]()
|
![]()
|
How It Works:
The term ".22" or ".224" covers all of the normal 22 centerfires, which all use 0.224-inch bullets with rare exceptions. For example, the .222, .223, 5.56, 5.7mm, .225, and other cartridge names all use a .224 diameter bullet regardless of what the cartridge is called.
A .22 LR case draws out to make a jacket suitable for 45 to 65 grain bullets depending on how much lead you put into it. The heavier weights become lead tip, the lighter ones are open tips. The rim is unfolded and ironed smooth. It isn't "cut off". This is actually how the very first centerfire 22 bullet jackets were made by Harvey Donaldson of the "Donaldson Wasp" fame, before any of us were alive!
You can also use regular drawn commercial jackets available from Corbin and other suppliers with the same dies, possibly with a different core seating punch to fit the thicker wall jacket's ID. And once you learn how to make a 224 bullet, the same process and tools with appropriate diameters are used to make any other caliber! Learn one, you have learned it all from .104 to 20mm. Minor variations such as rebated boattails, tip inserts, and making your own tubing or copper strip jackets don't really change how things are done in any major way.
An 6mm kit can also be ordered, KIT-243R, which makes 65 grain lead tip bullets using fired 22 cases. A different size jacket maker and swage dies are used but the same size core mold works for either caliber. Longer, heavier jackets can be purchased ready-made from Corbin, or an optional 6mm jacket maker using 22 Magnum cases can be ordered.
An extra core seating punch is provided for use with Corbin bullet jackets. Open tip, lead tip, and full metal jacket styles can all be made with the set. Other brands of commercial jackets might require a different, optional core seat punch. Some jacket with thicker walls might require a smaller core swage die or smaller diameter core mold -- always send sample jackets for testing and measurement so the proper size tools can be provided for use with them.
For additional weight control with the lower priced reloading press kit, the optional CSW-1-R core swage die can be ordered, which bleeds off surplus lead from the lead cores, leaving a fixed volume of lead on each stroke. The weight can be set by you by the position of the die in the press head. (The core swage is included in the KIT-224S, for the S-press.)
Use any sturdy reloading press that accepts 7/8-14 threaded dies and has a t-slot ram that takes standard RCBS type button shell holders with the Corbin KIT-224R or KIT-243R. Progressive style presses, turrets and other special designs that do not accept a standard RCBS type button shell holder are not suitable.
If you do not want to melt scrap lead for your cores, you can instead choose a spool of lead wire (.185 diameter) and a Corbin Core Cutter (PCS-1). Or get both so you can decide what to use depending on the time you have that day! A core mold costs just about the same as two 70,000 grain spools of wire and a core cutter. A single spool of wire makes, on average, about 1,550 bullets. (Subtract jacket weight from desired bullet weight, and divide the answer into 70,000 for number of bullets per spool of wire.)For a high quality, professional looking lead tip, an optional LT-1-R 224 6-S lead tip forming die can be used in a reloading press, or the LT-1-S 224 6-S lead tip die can be ordered for use in the Corbin S-press.
A lead tip finishing die reforms the somewhat blunted lead tip for a professional appearance. You can make lead tips by putting more lead core into the same length of jacket, so that the lead extrudes from the end of the jacket when you form the ogive. Note that a lead tip finishing die is always used AFTER forming the ogive in a point form die. Don't confuse a point former with a lead tip finisher!
To make a lead tip with less weight, put one of the 3/16-inch diameter "bullet balls" into the jacket first, with a lighter core on top. That moves the lead forward, so the same amount will now be available to make lead tips without any extra weight. Bullet balls are available from Corbin in packages of 1000, and are used for both balance and weight control, for making accurate super light bullets, and for making polymer rounded tips.
Questions About Rimfire Jacket Bullets
|
How to Swage .224 Bullets
|
Corbin Manufacturing & Supply, Inc. |
Start writing here...
Make FREE 22 or 6mm Bullets!