PF-1-S or PF-1-H Point Forming Dies normally have a spring wire ejector that is retracted from the die cavity, and does not contact the bullet during swaging. It pushes the bullet out of the die on the down-stroke of the ram.Special PF-1-SC or PF-1-HC dies can be made with bleed holes to swage a lead bullet and adjust the weight in one pass. These dies require a pressure-sealing ejector to stop lead from flowing up the ejection pin hole. The internal punch is synchronized with the exact die cavity depth, to form a seal exactly at the cavity tip.
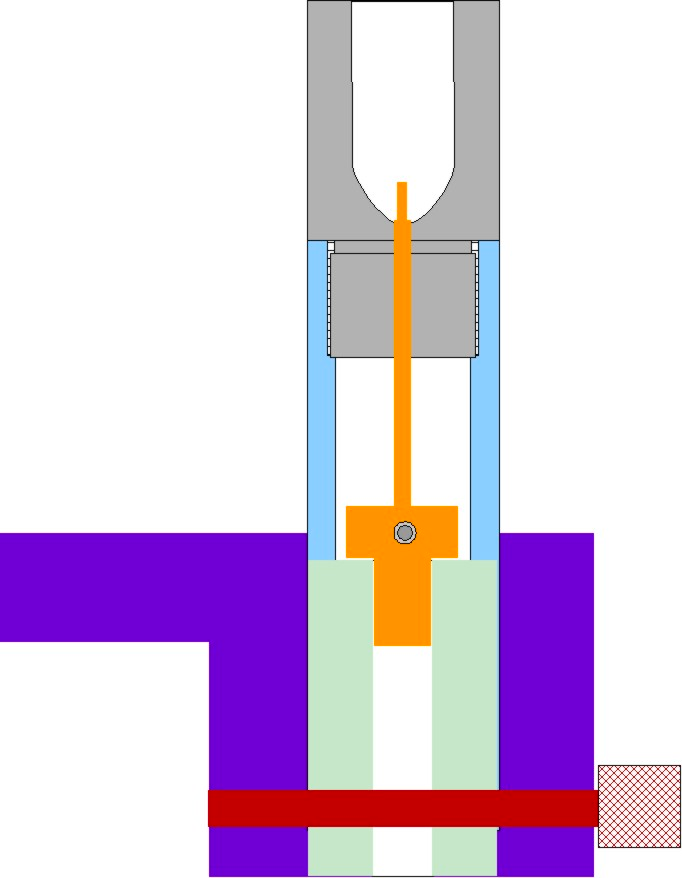
Tip-seating PF-1-ST or PF-1-HT dies have two ejectors. One is synchronized, and has a cavity-forming probe on the end to accept the stem of a metal tip insert. The other is not synchronized and has a cavity of its own to push a sharp metal tip bullet out of the die. The bullet is formed with two passes in the PF die, one to make the stem hole and the second to insert the tip.
In all PF dies, internal punch fits into the press ram and remains partly inserted into the die while swaging. (The external punch fits a punch holder in the press head, and pushes components into the die from the top -- when the ram retracts, the external punch remains in its fixed position while the die separates from it.)
When the ram is fully retracted to the "down" position, the internal punch is pushed to the open end of the die, ejecting any material in the die automatically. The length of the internal punch has to be the same as the die length to accomplish full ejection. In the CSP-1 press, a "stop pin" passes through a slot in the press ram. This pin is fixed to the frame of the press, so it does not move with the ram.
To insert a bullet into the die, first the ram is raised slightly. This takes the die up, while the punch still rests on the stop pin. The bullet or other component can now be put into the die, even though the ejection pin is still partly extended into the cavity. As the ram continues up with the die and bullet, punch head is picked up by a shoulder in the ram, lifting the punch up and off the stop pin. Now the ram carries the internal punch upward in a fixed position relative to the ram. The punch can only drop back as far as the shoulder. The distance from the ram shoulder, and also from the bottom edge of the punch head resting on that shoulder, to the end of the punch diameter sealing the ejection pin hole in the die, is the sync length.In the CSP-1 press, as the ram goes up along with the die, the internal punch is picked up by the shoulder inside the ram. As long as the ram is moved far enough up so that the punch head is resting on this shoulder, the other end of the punch (the tip) should be synchronized with the die cavity, sealing the end of the cavity. If the punch length is slightly too great, or if residue should fall into the ram and become stuck to the shoulder in the ram, the punch tip will not be exactly matched to the end of the die cavity. It will project into the area where the bullet is formed, and will make a large diameter hole in the end of the bullet (in addition to any smaller hole that is supposed to be formed by a smaller diameter projection). If the punch length is too short, it will not match the end of the die cavity and will leave a tube or projection on the bullet tip, where the core flows up the ejection pin hole.
Bear in mind that the CSP-1 press has a different design from the CSP-2 and Hydro Press in regard to the retraction mechanism. The CSP-1 has a retraction pin (stop pin) that is fixed to the press frame. The CSP-2 and Hydro Press use a spring-loaded retraction pin that moves in the same slot in the ram as a knock-out bar. The retraction pin, and the spring that pushes it down, pushes the punch head against a shoulder in the ram when the ram is raised. But the knock-out bar stops against the press frame during the down stroke, and picks up the support for the punch head, lifting it off the shoulder as the ram continues down. Since the ejection pin head length plays a role in positioning the punch relative to the die cavity, there are two dimensions which affect the synchronization of the punch tip with the end of the die cavity, not just one.
Sync punches in point forming dies can be used to seal pressure so that a lead bullet can be formed and the weight adjusted with bleed holes in the die walls. Whenever a point forming die is used to create a smooth ogive lead bullet, especially one with bleed holes, the ejection pin needs to be a synchronized type. The ejection pin hole in a standard point form die is drilled to guide a spring wire ejection pin. But the pin doesn't contact the bullet until it is time to eject. The die is not pressurized to flow lead to the tip, but only to shape the ogive. With a sync ejector point form die, the ejection pin hole is usually larger (.157-inch diameter is often used) and the ejection pin hole is closely fitted so lead cannot flow around the pin. The precise fit and exact matching of length to die cavity takes additional work, so the die costs more than a standard point former.
A PF-1-HC or PF-1-SC "custom" point forming die that has the sync punch option is marked with numbers that refer to the "sync" length. The die is only used with the specific punch length and size built for it. If the punch is lost or damaged, it is necessary to provide two numbers for -S type dies, and three numbers for -H type dies in order for the die makers to build the correct replacement punch. The numbers are:
- Diameter of the punch (typically on the order of 0.157, or 0.160, although some calibers and tip designs use other diameters).
- Sync length, which is the length from the full diameter tip of the punch (not including any reduced HP tip portion) to the back side of the punch head.
- For -H punches only, the third number is the overall punch length from head to full diameter tip (not including any HP projection).
![]() ![]() ![]() There are two kinds of metal tip inserts offered. One is the ULD-TIP. This is an ultra low drag nose design used for long range rifle bullets. It is not the same thing as the standard ULD ogive shape, but is a hybrid or combined ogive shape that varies with the caliber. It blends a tangent curve with a secant and spire shape so that two sizes of tips can be used for a range of calibers. The TIP-30-5 refers to the smaller ULD-TIP shape, packaged in bags of 500, and used for calibers from .284 to .338. It can be used for larger calibers as well, depending on the desired weight and appearance. The TIP-50-5 is a larger version with the same angle, used primarily for 50 caliber bullets but can also be used for calibers as small as .338 (with a larger portion of the ogive being the tip). ![]() The TIP-45-5 is called the "PIN POINT" tip. The die for the PIN POINT and the one for the ULD-TIP do not have the same shape for the same caliber, and the tip inserts do not interchange in the same die. Always use the correct ejector punch for a given die, and the matching tip inserts. Mixing punches and dies does not work. Not only are the punch lengths matched to a specific die cavity depth, but the style of tip is matched to the punches and the die shape. ![]() ![]() |
Corbin Internal Punch Synchronization Guide