The amazing perfection of properly swaged lead bullets can be seen in this photograph. New bullet makers have called to ask what the "bright steel thing" that looks like a bullet is doing in the package. They have a hard time believing it is a test sample of the bullet they can make with the die set, until we ask them to try to pick it up with a magnet or dent it with their thumb nail!
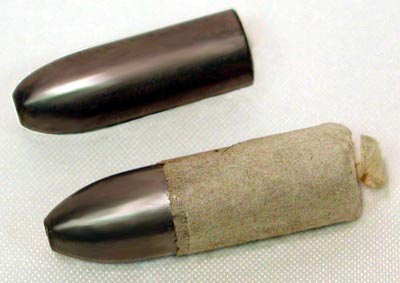
Bullets can be swaged as round balls, smooth sided for dry film dip or spray lube, hollow or cup base, heel or flat base. Dies range from the simple PRO-SWAGE for your reloading press, or the single LSWC-1-S or LSWC-1-H type for Corbin presses, to multiple sets for more complex finned slug designs. Prices start from under $300 depending on the specific bullet and the tooling needed to form it. Often there are several ways to achieve the same goal, with different costs traded against versatility or operating time. To read about replacing your cast bullet with a swaged one, see Replacing Casting with Swaging. | |||||
Lead Sources![]() Because of the infinite variety of possible alloy mixtures, and the excellent results with pure lead core bullets, Corbin only stocks pure lead wire. A lead wire extrusion calculator program, DC-LEAD, is available from Corbin on CD-ROM. It calculates volume, length, pressures, and even the size of equipment needed, including adjustment for alloy hardness. You can also use your own soft lead cast in Corbin core molds (CM-4a), which makes four adjustable weight cores at a time. Lead wire is cut to precise length with a Corbin core cutter (PCS-1 up to .365 diameter wire, PCS-2 for up to .430 diameter). You do not need a core cutter if you use the core molds, because the core length is set by the adjustment of the mold. The quality of lead core can be the same whether using wire or cast cores, depending on the consistency of the lead. Lead wire is a more assured purity than scrap lead, in general, since the analysis is known and consistent from spool to spool.
Lead wire larger in diameter than 0.430 inches is difficult to coil on reasonable sized spools, hard to straighten and difficult to cut, so very large lead cores are usually cast (in the .50 to .75 diameter range, or above). Lead wire smaller than .125 is available but it is much more difficult to extrude (pressure is an inverse square function of wire diameter with a given size starting billet of lead) and coiling requires special handling to avoid stretching and breakage. Therefore, the cost is somewhat higher for small diameter wire. Corbin offers 0.100 special size lead wire for calibers such as the .123 lead and .142 jacketed. This is the LW-10S (in 70,000 grain spools) and LW-40S in cartons of four spools. The convenience of cutting wire instead of casting tiny cores far outweights slightly higher cost, for most bullet makers. In 0.100 diameter, the LW-10 wire will make nearly 10,000 7-grain .12 caliber pellets or 15-grain jacketed .14 caliber bullets (since the jacket weighs nearly as much as the core). |
The lead wire diameter needs to be small enough to fit inside the core swage die, which adjusts the weight while expanding the core. The diameter of the lead core must fit inside the bullet jacket, which must be slightly smaller than the caliber before the core is seated. Since the jacket wall can be 0.035 inches (copper tubing jackets), or 0.026 inches (many commercial drawn jackets), or just about anything else, the choice of wire size for a given caliber is not fixed. It can vary widely with the jacket. Therefore, the starting point for determining core diameter and wire size is the choice of jacket. General Guidelines for Wire Size:
| ||||
Lead Hardness Hard lead can be swaged in some type -H dies, medium-hard lead in some -S dies, and soft lead in the all the dies. (Dies that swage hard lead can, of course, handle the much lower pressure involved with soft lead). Every time you double the Brinnell hardness number (Bhn), you increase by four times the amount of swaging pressure required. For this reason, a Bhn of 8-10 is usually considered maximum for the medium diameter (-S) dies without bleed holes, 6-8 with bleed holes. Hard lead, for swaging purposes, is anything above Bhn 10. Medium hard is from 8-10, and soft is from 5-7. The limitations of swaging hard material are not just the hardness, but the shape as well. A long, pointed bullet takes more pressure to form than a round nose. A bullet with many thin or sharp edges, hollow cavities, hollow bases with thin skirts, or other areas where lead will be squeezed into sharply defined acute angles or thin sections, will be much harder to form than a bullet with gently rounded curves, and no thin sections to fill in. Therefore, it isn't possible to make a true blanket statement about what hardness works and what doesn't. Sometimes we can work with a very hard to flow material, such as silver or aluminum, and make it work in some dies but not in others. Actual hardness isn't always related directly to the ability to extrude or flow under pressure. Gold is quite "soft" in the usual lexicon of metalurgy, and can be rolled or pounded into sheets thinner than paper. But it is difficult to swage, requiring many times the pressure of an apparently equal hardness of lead. If you have a requirement that uses hard to flow materials, contact Corbin first before attempting to swage it. Send us a sample, if possible, and let us break OUR dies, instead of breaking your own, if it comes to that! Swage dies are made primarily for swaging materials that flow exactly like pure lead. It doesn't really matter how hard or soft the material is, so long as it will flow under pressures that are safe with the dies. Bhn 8-10 is fairly typical of wheel weight hardness, which can still vary over a wide span from pure soft (Bhn 5) to very hard (Bhn 15+). A Core weight/length chart is available to download or print, showing standard wire sizes, core weight in grains and length of core to provide that weight. A program called "DC-LEAD" is available from Corbin to calculate lead wire extrusion pressures, weights, lengths, ram thrust, drive cylinder sizes and oil pressures required, as well as the core weight and length for any size wire. Corbin's World Directory of Custom Bullet Makers has listings of nearly 200 sources of lead, including most of the world's largest suppliers, who can tell you where to purchase lead wire or ingots from their distributors and "fabricators" (as the makers of lead wire are called). In addition, many custom bullet makers who have the Hydro-Press offer extruded precision lead wire to other bullet makers, and this is noted in the listings in this useful reference book. | ||||
Core Cutters Corbin makes the PCS-1 and the PCS-2 lead wire or core cutters. The PCS-1 cuts wire from .100 to .365 diameter and comes with several hardened insert die pairs (use the one closest to but larger than the wire diameter you need to cut). The PCS-2 Magnum Core Cutter cuts any size of wire up to 1/2-inch, but is most commonly used for .430 and .390 diameter wire. It comes with a pair of hardened dies for the wire size of your choice. Additional die pairs can be purchased for other sizes. The PCS-1 and PCS-2 both use a threaded stop located on a bar below the hole in the pair of hardened dies. The dies line up over the stop, and lead wire is pushed through the dies until it stops against this adjustment screw, which sets the weight of wire to be cut off. Then, with gentle pressure on the wire, the handle is moved back and forth to chop off pieces of wire to the desired length. The tools mount, by one end, to the work bench. The other is free to swing horizontally, and the cut pieces drop into a box put below the tool. |
Lead Wire Extruders![]() The length of wire depends on diameter. The same volume of lead that is in the 3/4-inch by 4-inch billet is convered to whatever length holds the same volume at the wire diameter. This can vary from several feet to dozens of yards. The wire comes out fast and is heated by friction, so gloves should be worn to avoid burns. Corbin's wire extrusion software calculates the length, weight, and pressures instantly. Smaller diameters, up to .185, can be extruded in the Corbin CSP-1 or CSP-1H press. The CSP-1 hand press uses the LED-2-S extruder, which accepts .430 diameter cut wire and turns it into the desired diameter from 0.100 to 0.185. The LED-2-SC extruder is a longer version designed for the Hydro-Mite press only. It can extruder longer pieces of wire than the few inches produced per stroke in the hand press. ![]() Additional billet mold tubes and bases are available to increase your production. Usually two tubes are alternated on one base, but you can use three or four tubes, filling and removing them to cool, slipping another on the base, pouring, removing, etc., for higher production. A second or third base really lets you make lots of lead billets in one sitting. (Wear eye protection and heat resistant gloves when working with hot lead. Make sure there is good ventilation and no chance of water drops getting into the lead pot. Working outdoors is good, but having a cover against possible rain or a screen against bugs (which can fall into the pot and cause the molten lead to erupt) is advisable. The range of diameters which can be extruded in the LED-1-H with a CHP-1 Hydro Press is from 0.170 to 0.430 inches. For sizes smaller than 0.170 inches. Smaller diameter wire can be extruded by using a special version of the LED-1-H with a smaller bore size, to apply the ram force to a smaller area and increase the internal pressure. Although not listed, the LED-1-HC custom version of the extruder is built to your custom order for wire sizes under 0.170 inches, such as 0.150, 0.125, or 0.100 diameter. Smaller billets of lead are required as well. | |
Lead Hardness Test Here is a simple way to test the Bhn number of unknown lead samples: all you need is a caliper, two bottle caps, a vise, a 5mm diameter (aprox. size) ball bearing, and a known pure sample of lead (Corbin can furnish pure lead of 99.995% Pb with trace silver).
Here is the formula: H = 5 * (D1^2)/(D2^2) ...where H is the hardness of the unknown sample in Bhn number, D1 is the diameter of the indentation formed in the known pure lead sample, and D2 is the diameter of the indentation in the unknown hardness sample. Why This Works: The reason that you will always get a number of 1 or greater is that the ball will always go further into soft material (pure lead) than it will into hard material (any alloy of lead with tin, bismuth, antimony, etc.). Therefore, the diameter of the dent will always be smaller in the unknown sample, if it is harder than pure lead, or the same as the known pure sample, if it is also pure lead. When you divide a smaller number into a larger one, you always get something greater than one for an answer. Brinnell numbers are all greater than one. You must multiply the answer by 5 because this is the adjusting constant for pure lead, which is Bhn 5 hardness. This method is as accurate as your sample purity and your ability to read the diameter of the dent. A smooth surface is necessary so you can get a clean diameter to measure. A rough surface will throw off the answer because you may not get a true diameter to measure, if one side of the lead surface is higher or wavy. But in general, this is as accurate a method as any that uses tools which cost less than $500. A reading with an accuracy of only Bhn plus or minus 0.5 will be more than sufficient for purposes of swaging. When the Bhn number actually increases from 5 to 10, or doubles, the pressure goes up by a factor of four, or the square of the increase in hardness. A number of 5-6 Bhn is close enough to be called pure for swaging purposes. A number of 10-12 is close enough to be considered about "medium" hardness or suitable for -S dies. A number of 18-20 is hard enough to be considered strictly for the -H type hydraulic dies even if used in the CSP-2 hand press. | |
Casting Lead Cores You can cast your own scrap lead in Corbin Core Moulds, model number CM-4a. The CM-4a is available in standard sizes up to .430 diameter, but can also be ordered in custom sizes in nearly any diameter up to .625 inches. The mold is made with four adjustable weight casting cavities, except for large custom sizes, which are made with three cavities. The standard design of mold is built with a solid block of cast iron having four bored holes fitted with pistons, very much like a straight line car engine. A long steel sprue plate pivots over the top of the mold, similar in some ways to the head on an engine block. The sprue plate is moved to one side to cut off the four small connecting links between an open "bathtub" at the top of the sprue plate, and the lead in the cylinders. When the sprue plate is moved to the side on its pivot, a rest plate or bar at the bottom of the mold can be pushed up to eject all four of the lead cores at once. The sprue plate is then swung back into position, so that the four small holes connecting the depression machined into the top will align again with the four cylinder holes. A pick or needle nosed pliers can be used to put the remaining sprue (left over lead in the open top of the sprue plate) back into the lead pot. The mold can be adjusted for length of core, to set the core weight. This is done by adjusting the position of the nuts which support the rest plate, which both ejects and supports the pistons. Lowering the rest plate position also lowers the pistons, so the cylinders hold more lead. Raising the rest plate reduces the core weight. Weight control of around 1 to 2% of total bullet weight is achieved. For more precise weight control, a core swage die is used to slightly reduce the cast core weight while making it more uniform. Weight tolerances of less than 0.5% of total bullet weight can be achieved with the core swage step. For most purposes, a 1-2% variation in bullet weight makes no difference. For benchrest shooting, the tightest possible weight control is desired (although below 0.5% of total bullet weight, the effect on bullet group is virtually non-existent). The core molds are not made with a combination of sizes in one block, nor can the molds be changed from one size to another. However, this also means there are no removable cylinders to become loose from repeated heating and cooling, making the CM-4a a more reliable product as well as extending its range of sizes while reducing the cost. | ![]() ![]() ![]() You can also extrude your own lead wire, making a profitable secondary product to sell. The LED-1-H lead wire extruder fits the Hydro-Press. It is not practical to extrude lead wire in a hand press of any size, except for the tiny .14, .17 and 5mm calibers. You only get a few inches of lead on each stroke of the press, whereas with the power machines, you can get yards of lead on a single stroke. ![]() |
Paper Patched Bullets![]() ![]() A more nearly perfect bullet can be made in two operations, using a separate "core swage" die and a second "core seating" die. By separating the weight adjustment step from the nose and base forming step, long hollow cavities and sharper noses can be formed more precisely than if the pressure is being released through the bleed holes at the same time as the lead is trying to fill out the complex, small shape of the nose or cavity. In very small bullets (pellets) or with thin skirted hollow base bullets, this is highly recommended over a single die operation, but both usually work. The two die operation is available in Corbin presses and dies made to fit them. ![]() These bullets can also be made in a style that has a tangent ogive (no shoulder). This requires at least two dies. The first die is a core swage or a LSWC-1 style (for this application a CSW-1 core swage and a LSWC-1 lead semi-wadcutter die are used the same way). The second die is a point forming die, which has the curve of the bullet nose formed in the die rather than a punch. This is slightly more expensive than using the two straight-through dies, because a point forming die is harder to make. But it eliminates a slight drag effect on the shoulder and thus the bullets have higher BC for long range or high velocity shooting. A paper patched bullet is always made smaller than the groove-to-groove diameter of the barrel. For example, if a normal jacketed bullet would be .458 diameter for the .45-70 barrel, then a paper patch bullet for the same gun might be made .448 to use with 1.5-inch thick paper wrapped around twice. Or it might be made .451 or .452 diameter to be used with thinner paper. The diameter you want depends on both the groove depth and the bore size, and the paper thickness. A common formula is to use groove to groove diameter minus four times the paper thickness. ![]() A variation on the paper patch bullet is the TEFLON TAPED bullet: instead of using paper after swaging, a wide 3/4 inch teflon pipe tape is used around the bullet. If you first swage the bullet almost to size, perhaps .005 inches smaller, and then wrap it and swage again in a slightly larger die (final size), the lead will gently push out against the tape. It could otherwise be pulled off if you tried to put the bullet back into the same size die that built it without the tape wrap. This method uses two dies, but you can make one of them the final size for a lead bullet without a patch and the other .008 inches smaller so it can be used with regular paper patching also. This gives you three different bullets with two dies (base guard or knurled lead in the big die, paper patch in the small die, and teflon patch using both dies in succession). For more info, go to Paper Patch page. | |
Base Guard Bullets A Base Guard is a trade-marked name for Corbin's fouling-scraper disks attached to the bottom of the bullet at the same moment the bullet is formed. These disks form a sharp burnishing tool edge, which scrapes fouling out of the bore with every shot. The disk rotates with the rifling, regardless of whether the body of the bullet skids or fails to turn in the rifling, and thus seals the bore against powder gas (unlike a gas check, which is crimped on the surface of the bullet and cannot turn separately from it while in the bore). Base Guard disks eliminate the need for lubricant or paper patching. They cannot be used with a hollow, boattail, rebated boattail, or any other base style except the flat base having a BG dimple to allow lead to flow through a hole in the disk, and attach by forming a rivet head on the opposite side. Their advantage is extreme speed of manufacture, high degree of accuracy, automatic cleaning of powder and lead fouling from the bore, and elimination of traditional lubrication. Base Guard disks are applied in either the LSWC-1- type of die, or in the two-die operation where a PF-1 is used. If the two-die operation is used to eliminate a shoulder, then both dies must use a punch on the base end that supports the rivet head shape holding the disk to the bullet. | ![]() ![]() |
Knurled Bullets Knurled bullets hold far more lubricant in contact with the bore than a grooved, conventionally lubricated bullet (such as most cast bullets). The surface is covered with a fine diamond pattern, like reversed checkering, that holds a conventional or a dip-type lube against the bore, like a waffle holds syrup. It's easy to apply knurling to any finished lead bullet with Corbin's HCT-2 Knurling tool. Just put the bullet on the two rollers that make up the V-way, close the handle and turn the crankshaft one or two revolutions. Then spray the knurled bullet with a dry film lube, or pour a conventional Alox-type lube around a pan of them and use a closely fitted tube or case to cut them out of the lube. Other methods include dusting with graphite and/or moly disulphide powder and then re-swaging to trap the lubricant in the knurling under high pressure. Re-swaging brings the size of the bullet back to precisely the right diameter (knurling increases the effective diameter slightly). | ![]() |
Grooving Tool Any lead bullet can be grooved with Corbins HCT-3 grooving tool. The grooving tool places two serrated grooves on the bullet, at the same time. You can move it and place two more if you wish. The most precise method of lubricating and forming these bullets is to use two different size dies. First, the bullet is formed as a parallel sided cylinder that is .005 to .010 inches smaller than final size. The cylinder is knurled or grooved, and then lubricated by dipping, pouring, or tumbling with appropriate liquid, wax, or powder lubricants (all have been used with success). The grooving process expands the diameter slightly, and the method of lubrication application can add dimensional changes of its own. Then the lubricated, grooved cylinder is put into the final die and expanded slightly to the correct diameter under tons of pressure. The nose and base are usually formed at this time. By using a two-diameter process and applying lube in the middle of the operation, the bullet comes out with lubricant applied under extreme pressure, making it far more even and free of voids and air pockets than the typical low pressure lubing operation. The final roundness and diameter are nearly perfect with this operation, as compared to cast bullets. Precision is greatly enhanced. | ![]() ![]() |
Spray-On Dry Lube Corbin offers a spray-on, quick-dry moly lube for lead bullets. The pressurized spray can will coat hundreds of bullets with a light brown colored dry film that protects the bore from leading. Corbin's Moly Spray is formulated to apply a clean, hard coating on the bullet that increases the slickness (reduces friction) of the bullet passing through the bore. The dry film is thin enough so that it does not prevent the bullet from fitting the chamber or cartridge. It must be used in a well ventilated area because of the flammable propellant in the spray can. No open flame, smoking, or sparking machinery should be present when applying the lube (same precautions as you would use with spray paint). The lube does not soften black powder fouling. If you are shooting black powder, you can use a combination of "hard" wad and "grease" wad, both of which can be made for your gun, either for cartridge or muzzle loading, using a Corbin DCD-1-S or DCD-1-H Disk Cutter Die. The die is similar to the BGK-1-S or BGK-1-H Base Guard die, with a slot through which you pass material as you move the press ram in short up and down strokes to punch out disks. Two kinds of material are punched with the tool. Felt upholstry padding, in a half-inch thickness or less, is turned into felt wads. Stiff "nitro" cards or "hard" wads are made from bristol board or other stiff cardboard. After punching out a number of each kind of wad, the felt wads are placed in a pan with hot Alox-Beeswax lube mixture (or use your favorite grease normally applied to the bullets). The wads are slowly stirred with the melted lube until they are saturated. Then they are removed, drained briefly to remove surplus grease, and allowed to cool. The hard wad or "nitro card" is placed in the barrel or cartridge first, on top of the powder. The fit is snug, to prevent lube from contaminating the powder. To make sure that the grease won't migrate through some grades of cardboard, test it first for "soak through" by placing some of the lube on one side and periodically checking for seepage. If necessary, spray one side of the cardboard with a grease-proof shellac or enamel paint and allow it to dry before punching more wads. The grease wad is placed on top of the hard wad, so that when the gun is fired, the hard card acts like a piston and compresses the felt, squeezing lube against the bore. The lube should be a type that softens the black powder fouling, to be effective. The bullet may not require any lubrication, with this system. | |
Start writing here...
About Corbin Swaged Lead Bullets