Now available in 115-120v 60hz or 220-240v 50hz!
Reversible rotation, center-pause/off switch prevents accidental reversal. Continuous duty production, up to 30 bullets/minute.
Cartridge cannelure version
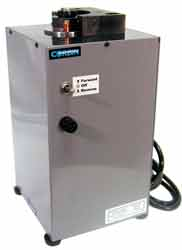
HCT-1 Cannelure Tool![]() ![]() |
The PCM-2 power cannelure machine, introduced in 2003, replaces the earlier PCM-1, and is available in both 120 and 240 volt 50/60 Hz versions for domestic and export purposes. The machine is approximately 20.5 pounds of high powered production capability, in a 6 X 7 footprint with 11 inch height. The machine is used throughout the firearms industry to put precisely adjustable depth and position cannelure grooves on finished jacketed bullets, grooves on cartridge cases, lube grooves or knurling on lead bullets, and even for such applications as knurling fishing rod ferrules or sealing copper tubes with a rolled crimp to hold a copper disk in place. It is part of the production line in major bullet factories, as well as being found on the R&D lab benches and in the shops of custom bullet makers.
![]() ![]() |
The standard cannelure is .050-inches wide with serrations. Custom wheels without serrations and wheels with more than one groove are possible, but bear in mind these limitations:
- The driving friction to turn the component comes from the teeth on the cannelure wheel. If there are no teeth, then we must rely on friction of contact alone. This is not quite as reliable as having actual serrations on the wheel, although we can usually make it work.
- The total area of all the cannelure grooves compared to the area of support is what keeps the grooves from simply being "ironed out" by the supporting back plate. Thus, you should keep the width and number of grooves at a minimum that will do the job, so there is at least 300% more support area than there is grooved area.
- The depth times width times number of grooves is the amount of material that is displaced, which has to go somewhere. Most cannelure grooves work fine with .010 to .015 inch depth and .050 width, and with one to three grooves per inch of shank. But when you exceed this volume of material displaced, the bullet can be distorted (enlarged or elongated). You can sometimes get away with this by grooving the bullet while it is in an intermediate manufacturing step, prior to final diameter, or by forming an undersized bullet, grooving it, and then expanding it to final size to restore the proper diameter and roundness. Lubricant applied to the grooves keeps them from collapsing under the swaging force in the final step.
- A deep hollow base bullet, such as a Minie Ball, may present difficulties if you want to put deep grooves on the thin skirt section. The pressure required to emboss the cannelures into the surface may crush the thin lead skirt. Solutions usually involve moving the grooves higher on the shank, so that the skirt is not under pressure, using more shallow grooves, or swaging the bullet with a small pilot hollow base, forming the grooves, filling them with lubricant and then finishing the hollow base in the final die (since the lube will prevent the grooves from collapsing under the swaging pressure).
Unlike previous models which were only available in 115 volt 60hz, the new version is available in either 115-120 volt 60hz (for use in the USA and countries using the same power systems) or in 220-240 volt 50hz for export. (Please specify the voltage and frequency, unless you want the standard USA version.) The PCM-2 also features a center-off positive stop reversing switch, which prevents the direction of rotation from being accidently reversed by bumping the switch. Reverse rotation can be used during setup.
Select to see wiring for 110 or 220v versions.
Start writing here...
About Corbin Power Cannelure Machine