Corbin Powder Metal Tools:
Powder Funnel Assembly
The "Precision Funnel" solves the problem of how to accurately place a column of powdered metal into a bullet jacket, when the column of uncompressed powder is up to 100% taller than the jacket into which it must be compressed.
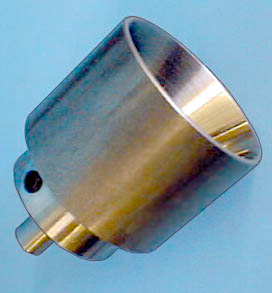
For filling bullet jackets, the funnel utilizes a machined steel, replaceable highly finished spout so the fine particles slide easily without sticking to the sides. The spout is made precisely to the same wall thickness as the bullet jacket to be filled, so that the core seating punch will seal the powder column and push it into the jacket without powder leakage. You can order the funnel (which comes complete with one custom made spout), and additional spouts later for other calibers and wall thicknesses of jacket. The spout is precisely matched to a given jacket wall thickness and caliber, but the funnel is the same for all calibers. An extra-long punch is available to fit the spout, because the standard core seating punch is generally too short to clear the funnel and still seat the core. The custom made punch is fitted precisely to the jacket ID, which in turn matches the ID of the funnel spout. | |
![]() | Powder is stacked in a column within the powder funnel spout and the bullet jacket. The spout is a changeable component, matched precisely to the wall thickness of the jacket (at the mouth). The powder is weighted or metered, then poured into the funnel top. For non-jacketed bullets or powdered metal core forming, a special core forming die with removable extension and long punch is used. The outside top edge of the die is precision machined to fit a recess in the bottom of a cylindrical funnel extension. The bore of the extension and die are aligned with high precision, so that the powder can be pushed down to less than 50% of its original height. |
![]() | The extra-long core seating punch compresses the powder down through the spout and into the jacket. Without the funnel and spout, the powder would simply stack on the jacket edge and not all of it could be pushed down into the jacket. When there is no jacket, the bore of the funnel and the bore of the die are aligned and made exactly the same diameter. Instead of a thin spout, the funnel is built as a cylinder with a recess that fits the top of the die. |
The edge of the spout lightly contacts the edge of the bullet jacket, when both are placed in the core seating die. The powder can then be dumped into the funnel mouth, and it is directed into a column that first fills the jacket, and then fills the neck of the funnel spout as much as necessary to hold the full powder weight. The special, long core seating punch, which fits precisely in the mouth of the bullet jacket, is then run through the funnel and into the die, compressing the powder ahead of it and packing it into the jacket. An optional Quick Change punch holder can be used with long bullets, to quickly remove the punch, in case the length of the funnel, punch, and jacket is too great for easy removal without unscrewing the regular punch holder. If Corbin Atomized Copper is used, the core is packed firmly and securely into a solid mass within the jacket and may be handled or turned upside down. Other powder metals may not stick together as firmly, requiring more careful handling. The funnel is made to meet specific client needs and is therefore made to order. The same funnel can be used with various jackets of different caliber, wall thickness and length, by purchasing additional removable "spouts" to match the jacket, and long core seating punches for different diameter jacket walls and calibers. The utility of the device lies in its precision O.D. fit to the die cavity, I.D. fit to the core seating punch, and consequent exacting match to the jacket mouth wall thickness (otherwise, the core seating punch would push powder metal past the various components and fail to achieve an adequate pressure seal). To purchase a powder metal seating package, it is necessary to supply Corbin with samples of the jackets to be used, powder to be seated, and a specification of the volume or weight of powder to be inserted. Armed with this information, a rapid method of filling and compacting the powder into the jacket can be developed. Point forming dies are mounted in the press ram so that the open end of the jacket faces down toward the die point. When the ogive is formed, the powdered metal core can be broken apart at the end and drop particles into the die (unless the open end of the jacket is sealed with wax or silicon seal, a plastic ball, or other means of preventing any loose core material from escaping). Therefore, Corbin can provide a special "upside-down" mounting for the hand press, or a special adapter and ejection unit that mounts the point forming die in the press head, so the bullet can enter with the open jacket end facing upward. These methods are not required if a drop of candle wax, silicone seal, a plastic bullet ball, or some other method is used to seal the jacket. For further information, contact Corbin with specific requirements. |
Start writing here...
About Corbin Powder Metal Tools