A tool to put two 0.075-in wide grease grooves, 0.225-inches center to center, on smooth-sided, swaged lead bullets is now available from Corbin. The HCT-3 gooving tool comes standard with a double-groove wheel to roll up to 0.020-inch deep grease grooves into lead bullets from .172 to .720 caliber. The position and depth can be set by adjustable stops, or done by hand, with a couple of quick turns of a crank.
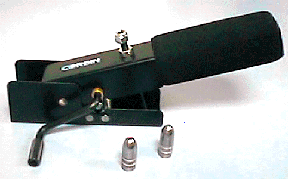
The tool has a comfortable expanded foam grip, hard chrome plated roller V-way to support the bullet, and a grooving wheel on a steel crank axel. The tool adjusts for various size lead bullets in the typical muzzle loading calibers from .375 to .720 automatically. By moving the pivot pin to an alternative set of holes (remove one pin retainer, slip the pin out and into the other set of holes), you can change the range to 172-458 diameter with an overlap in range from 375 to 458.
The grooving wheel (HCT-3W) is available as a separate part, to convert the HCT-1 cannelure tool into a lead bullet grooving tool. The wheel has two .075-inch wide straight knurled rings, with a diameter of about 0.8 inches. The space in between the two grooves is 0.15 inches. The wheel is secured to a flat machined on the crank shaft by means of a 6-32 set screw, located in the recess between the two embossing surfaces.
The area embossed by the wheel is wide enough so that the tool is recommended only for grooving lead bullets, and not for jacketed ones, since the force is spread over a large area. The contact area is 2 times 0.075 inches width or about 0.150 inches times the number of teeth engaged at any given depth. The force needed to emboss a copper alloy jacket is achieved by applying the same effort to a much smaller contact area (.05 wide single groove) on a hardened tool steel wheel, which concentrates the effort on a single 0.050-inch wide point of contact. The amount of contact area on the HCT-3 wheel spreads the force over too wide an area for satisfactory use on jacketed bullets. Too much effort is required to achieve the same embossing pressure as you get with the proper jacketed bullet cannelure tool.
Custom grooving wheels, with from 1 to 4 grooves machined on one wheel, can be made to order. The HTC-3C custom grooving wheel can have from one to four grooves, so long as the total width of all grooves does not exceed 0.25 inches (doing so displaces too much lead, requiring excessive effort and deforms the bullet when pressed in deeply enough to hold lubricant). The spacing from the first to the last groove cannot exceed 1.2 inches. The shape of the grooves can be beveled or straight on one or both sides. A drawing or sample bullet is needed in order to make a custom wheel. The spacing and width as well as groove shape should be specified on the drawing, if no sample is provided (hand-machined samples are adequate). A non-refundable deposit of 50% is required for custom work.
Corbin builds two other similar tools, the HCT-1 jacketed bullet cannelure tool and the HCT-2 knurling tool for lead bullets. The HCT-1 cannelure tool puts a single 0.050-wide groove on a conventional copper or gilding metal jacketed bullet or a hard lead bullet. The HCT-2 knurling tool applies a diamond pattern to the surface of a lead bullet, to hold far more lubricant than a groove. In addition, Corbin builds the PCM-2 Power Cannelure Machine, which can run over 100 bullets per minute. It is used by commercial bullet makers in their production lines. For prices on this and other Corbin tools, see the price list.
Start writing here...
About Corbin Muzzle-loader Bullet Grooving Tool